Around 80% of fires in hyperbaric chambers occur due to the presence of prohibited items in the chamber.[1] The NFPA recommends that hyperbaric facilities utilize the NFPA Risk Assessment Algorithm for assessment of dressings and items that have not been evaluated or deemed safe for use in the hyperbaric chamber.[2] However, several challenges prevent widespread use of the NFPA Risk Assessment Algorithm (see section 'Obstacles preventing compliance' in topic "Prohibited Item Risk Assessment"). Most importantly, completion of the current algorithm does not provide the necessary detail to identify the level of risk, the exposure potential, and the consequences if the item is allowed into the chamber.
HOW TO CONDUCT A RISK ASSESSMENT WITH THE GO/ NO-GO TOOL
The Go/ No-Go Tool allows hyperbaric programs to collaboratively create their own digital "use list" and "do not use list" (i.e., "Go/ No-Go lists"). As a result, clinicians can easily consult previous risk assessments and generate risk assessment documentation as required by the NFPA.
The instructions below illustrate how to:
- Step 1: Look up previous risk assessments
- Step 2A: Create a new risk assessment and documentation
- Step 2B: Copy and edit a public risk assessment
Step 1. Look up previous risk assessments
Table 1 below illustrates how to look up previous risk assessments.
Table 1. Step 1. Look up previous risk assessments
Process | Tasks | Rationale/Tips |
1. Search for the item in your facility private Go/ No-Go digital list | - Open the Go/ No-Go Tool
- Uncheck the 'public' check box to see your facility Go/ No-Go list (Figure 1)
- Search for the item whose risk needs to be assessed
Fig. 1. Uncheck the 'public' check box to see your facility private Go/ No-Go digital list
| - Note that if this is the first time using the Tool, you will not see items in your facility's Go/ No-Go list as it needs to be populated first
|
2. Search for the item in the public Go/ No-Go digital list
| - Open the Go/ No-Go Tool
- Confirm that the box 'public' is checked (Figure 2)
- Search for the item whose risk needs to be assessed
Fig. 2. Confirm that the box 'public' is checked to see the public Go/ No-Go digital list
| - A clip icon next to the item indicates that the respective risk assessment has a safety data sheet (SDS)
|
3. Decide if a new risk assessment is needed | - If you cannot find an existing risk assessment, go to 'Step 2A. Create a new risk assessment and documentation'
- If you found an existing risk assessment, go to 'Step 2B: Copy and edit a public risk assessment'
|
|
Step 2A: Create a new risk assessment and documentation
To complete a new risk assessment and documentation, follow instructions in Figure 3 and Table 2 (note that the 2 elements cover the exact same steps). For a recorded demo, watch the webinar "Performing risk assessments with the Go/No-Go Tool and the Burman Scoring System"
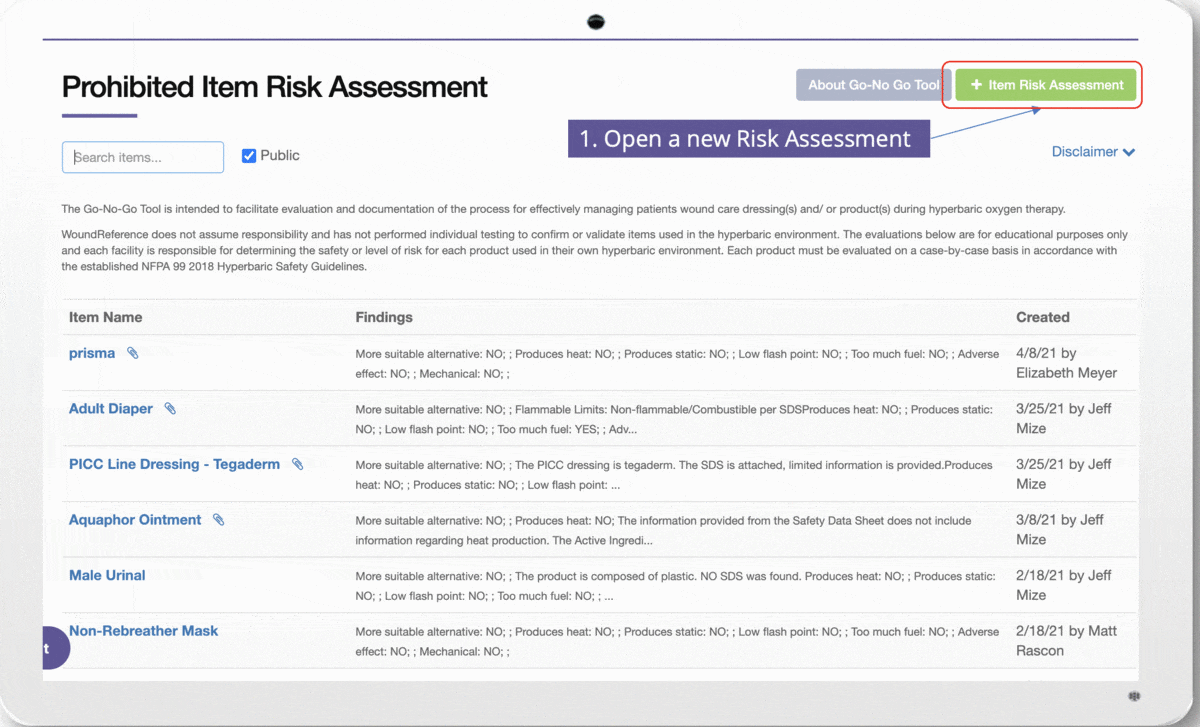
Figure 3. How to create a new prohibited item risk assessment (animated figure, wait 20 seconds for next screen)
Table 2. Step 2A: Create a new risk assessment and documentation
Process | Tasks | Rationale/Tips |
1. Open a new Risk Assessment
| - Open the Go/ No-Go Tool
- In the upper right corner, click on the green button "+ Item Risk Assessment"
- Add the Item Name
- Determine the chamber type
|
|
2. Search the internet for the safety data sheet (SDS) of the item being evaluated
| - Download the SDS from the internet, if available
- Click on 'Choose file' and attach the SDS
| - If there is no specific SDS for wound care/dressing items or the flash point information is missing, look for information on the individual components of the dressing or product
- For example: the SDS of petroleum gauze dressing (e.g. "Xeroform") does not have information on flash point. However, the SDS of petroleum jelly - one of its main components - provides information on its flash point
|
3. Evaluate the possibility of a more suitable alternative to the item being assessed
| - On the Go/ No-Go Tool, answer the questions:
- a) Can the wound orders be changed to a more desirable substitute that will eliminate or mitigate potential risks?
- b) Can the item be removed before the hyperbaric treatment, left off during the treatment, and be replaced after the treatment?
- If the answer is YES to any of these questions implement the more suitable alternative and proceed with HBOT. Document your reasoning.
- If the answer is NO to both questions, continue answering the next questions
| - If the product can be removed or replaced with a safer alternative, there is no need to perform a risk assessment
|
4. If there is no better alternative to the product being evaluated, evaluate the risks of allowing the item into the chamber
| - On the Go/ No-Go Tool, choose an answer to the questions below ("Yes", "No" or "No Info"):
- Does it produce heat (i.e. risk of fire and explosion)?
- Does it produce static (i.e. risk of fire and explosion)?
- Does it have a low flash point (i.e. risk of fire and explosion)?
- Is there too much fuel (i.e. risk of fire and explosion)?
- Are there any adverse effects (i.e. physiological risks)?
- Is there mechanical risk?
- For each question:
- If the answer is "No" proceed to the next question.
- If "Yes" or "No Info", quantify the risk by assigning a score to the 'probability' of an accident, the frequency of 'exposure' to the risk, and the magnitude of the 'consequence' should an accident happen. Describe actions to be taken to mitigate risk.
| - On the Tool, click on each question to see guidance on how to answer the question (also, see 'Appendix' below)
- Definitions:
- Probability of an accident: the likelihood that an incident or accident such as combustion due to fire/explosion, mechanical failure of the chamber, or undesired physiological event will happen as a result of exposure to the hazard.
- Frequency of exposure: how often will the facility, occupant or staff member be exposed to the hazard, if no mitigation actions are taken.
- Severity of potential consequences: severity of the outcome, should an accident occur.
- For more information, see section 'Types of Risk' in topic "Prohibited Item Risk Assessment"
|
5.Complete assessment
| - Upon completion of the assessment:
- Indicate if you would like the assessment to be public (i.e. visible to all WoundReference members) or private (i.e. only visible to members of your facility) by checking or unchecking the box 'Is Public' at the bottom of the risk assessment
- Click on the green button 'Submit' to see a summary of the results
|
|
6. Interpret results | - The Risk Score for each risk (fire and explosion, physiological and mechanical risks) is automatically calculated by multiplying probability x exposure x consequence.
- Compare the Risk Score of each risk (fire and explosion, physiological and mechanical risks) to the Risk Score range shown in the Table 1 "Magnitude Of The Risk: Consolidated Risk Score", and find the corresponding Risk Level
- For each risk, find the Risk Level and corresponding Risk Description. The Risk Description provides guidance on whether an item should be allowed in the chamber.
| - For details, see section 'The Burman RiskScoring System' in topic "Prohibited Item Risk Assessment"
- Evaluate the Risk Score for each risk (fire and explosion, physiological and mechanical risks) independently. The Risk Scores should not be added (i.e., do not add the Risk Scores and compare the resulting risk score to the ranges in the table)
- Upon interpreting final Risk Score, one might opt to further mitigate risks in an attempt to decrease the Risk Score. To do so, click on the green button 'Edit'. Document mitigation interventions under respective question (e.g. "Does it produce heat?") and review scores for the probability, frequency and consequence. Click on the 'Submit' button again to recalculate Risk Scores.
|
7.Generate documentation, if a decision has been made to proceed with HBOT and allow the prohibited item into the chamber
| - For each risk assessment:
- Generate documentation of the risk assessment: open the risk assessment summary, click on 'Print' and save as a PDF or print the form. Attach to the patient's medical record
- Fill out and sign the Prohibited Item Approval Form: Click on 'Authorization Form'. Fill out the prohibited item approval form and have it signed by the safety officer and medical director. Attach to the patient's medical record
| - As per the NFPA 99: “Physician and safety director approval to use prohibited items shall be stated in writing for all prohibited materials employed”.
|
Table 3. Magnitude Of The Risk: Consolidated Risk Score
Risk Score | Risk Level | Risk Description
|
>= 100
| 5 | Extremely dangerous: do not operate facility
|
50 - 99
| 4 | Very high: stop use of specific equipment, process or procedure
|
20 - 49
| 3 | High: Requires urgent attention; proceed with great care
|
5 - 19
| 2 | Medium: Attention needed but operation may continue
|
0-4
| 1 | Low: Acceptable risk but noted
|
Step 2B: Copy and edit a public risk assessment
One might wonder if it is appropriate to utilize the same risk assessment for an item of interest that was previously completed by another facility and is listed in the public 'Go/ No-Go List'. Hyperbaric programs are unique, with different strengths and risks. As such, it is recommended that each program copy and edit an existing assessment, and adjust the assessment to their own risks and mitigation interventions.
Table 4. Step 2B: Copy and edit a public risk assessment
Process | Tasks | Rationale/Tips |
1. Search for the item of interest in the public Go/ No-Go digital list
| - Open the Go/ No-Go Tool
- Confirm that the box 'public' is checked
- Search for the item of interest
|
|
2. Copy/edit existing risk assessment and adjust the risk scoring and mitigation interventions according to your facility's policies | - Click on the item of interest and open the existing risk assessment. Click on 'Print' to print out a hard copy. You will use it as a guide when re-creating your own risk assessment
- Create a new risk assessment - see 'Step 2A. Create a new risk assessment and documentation' above. As you create a new risk assessment, you can use the existing risk assessment of the same item as a guide. Adjust the "probability", "frequency" and "consequence" scoring for each risk, in light of your own hyperbaric environment and policies.
- Once completed, uncheck the box 'Is Public' at the bottom of the risk assessment, to make the risk assessment visible to members of your facility only (i.e., the new risk assessment will be part of your facility's private 'Go/ No-Go List')
| - Each facility is unique. Thus, it is recommended that each program copy and edit an existing assessment, and adjust the assessment to their own risks and mitigation interventions.
|
3. If needed in the future, retrieve custom risk assessment from your facility's digital Go/ No-Go List | - See 'Step 1. Look up previous risk assessments' above
| - As per the NFPA 99: This will prevent future duplication of effort. [1]
|
Examples
In this section, we will utilize the similar examples to the ones in the section 'The Burman Risk Scoring System - Examples' in topic "Prohibited Items Risk Assessment". However, this time we will utilize the digital Go/ No-Go Tool instead, which combines the NFPA Risk Assessment Algorithm and the Burman Risk Scoring System in a single process.
Example 1: Blankets for use in an oxygen-filled monoplace chamber:
- Determine the chamber type: monoplace chamber
- Attach Safety Data Sheet if available
- Is there a more suitable alternative? NO
- Answer questions below:
- Does it produce heat (i.e., risk of fire and explosion)? NO
- Does it produce static (i.e. risk of fire and explosion)? NO
- Does it have a low flash point (i.e. risk of fire and explosion)? NO
- Is there too much fuel (i.e. risk of fire and explosion)? YES
- Identifying the risk:
- Ignition source: blanket materials with the exception of those prohibited by NFPA 99 (e.g. silk or wool) require a significant amount of heat to initiate combustion.
- Assigning scores:
- Probability of fire: 1 (combustion unlikely)
- Exposure: 4 (less than twice a day)
- Consequence: 5 (potentially catastrophic based on history)
- Quantifying the risk:
- Risk Score: 1 x 4 x 5 = 20
- A score of 20 represents a medium fire risk, requiring the usual attention and discipline in operation
- Are there any adverse effects (i.e. physiological risk)? NO
- Mechanical risk? YES
- Identifying the risk:
- Lint production is based on the actual material to be used.
- Assigning scores:
- Probability of sufficient accumulation: 1 (failure unlikely)
- Exposure: 4 (less than twice a day)
- Consequence: 1 (slowed ascent rate due to outlet filter blockage, increase ascent rate where the exhaust regulator has lint on the seat).
- Quantifying the risk:
- Risk Score: 1 x 4 x 1 = 4
- A score of 4 represents a very low mechanical risk, easily mitigated through regular inspection and cleaning.
- Compare the risk score of each risk to Table 3. ‘Magnitude the risk: consolidated risk score’ above
- Address/mitigate identified risks: “With due attention to keeping out any known ignition sources – such as any substance that could have an exothermic reaction and resulting in temperatures higher than 140°F, selecting as blanket material that has restricted lint production and potential for static electricity generation, and through regular cleaning of the chamber, this risk can be rendered as ‘Acceptable’ - certainly no greater than typical scrubs used in a facility.”
- Document the decision process and mitigation interventions. Print a Prohibited Item Authorization form and have the Safety and Medical Directors sign it
Example 2: Petrolatum gauze dressing (e.g. Xeroform) for use in an oxygen-filled monoplace chamber
- Determine the chamber type: monoplace chamber
- Attach Safety Data Sheet if available
- Is there a more suitable alternative? NO
- Answer questions below:
- Does it produce heat (i.e., risk of fire and explosion)? NO
- Does it produce static (i.e., risk of fire and explosion)? NO
- Does it have a low flash point (i.e., risk of fire and explosion)? NO
- Flash point for petrolatum gauze dressing (e.g. Xeroform) is not stated in the SDS, however petroleum jelly is the main concern when using xeroform. Flash point for petroleum jelly is expected to be >212ºF/100ºC based on composition (thus flash point is not low). See attached SDS
- Is there too much fuel? YES
- Identifying the risk:
- Potential ignition source: petroleum jelly
- Assigning scores:
- Probability of a fire: 1 (combustion unlikely)
- Exposure: 4 (less than twice a day)
- Consequence: 3 (serious, disruption of operation)
- Quantifying the risk:
- Risk score: 1 x 4 x 3 = 12
- A score of 12 represents a medium fire risk, requiring the usual attention and discipline in operation
- Are there any adverse effects (e.g. physiological risk)? NO
- Mechanical risk? NO
- Compare the risk score of each risk to Table 3 ‘Magnitude the risk: consolidated risk score’ above
- Address/mitigate identified risks: “If there are no other alternatives, petroleum based dressings would be acceptable in the hyperbaric environment. The medical director should interface with the surgeon to see if there are alternative dressings”
- Document the decision process and mitigation interventions. Print a Prohibited Item Authorization form and have the Safety and Medical Directors sign it
APPENDIX
(back to text)
Table 5. NFPA risk assessment questions, guidance, risk identification/quantification
NFPA Risk Assessment Questions | Guidance on how to answer the questions |
Does it produce heat? | - Materials in a dressing can rapidly oxidize and produce heat (exothermic reaction) when exposed to additional oxygen. For example, air-activated heat patches (commonly used for pain relief) have been tested in hyperbaric environments.
- The average operating temperature increased from 48.1°C (119°F) in normobaric air to 121.8°C (251°F) in hyperbaric oxygen. In this circumstance, the patient would suffer severe burns, and the heat could ignite combustible material in the chamber.2
|
Does it produce static? | - All common textiles will contribute to static production. Wool and synthetic materials generally contribute more to static production than cotton. Although static charge is constantly accumulating, it will dissipate into the environment when humidity is present.
- At less than 30 percent relative humidity, static charge can accumulate faster than it can dissipate. At greater than 60 percent relative humidity, static charge is all but completely eliminated. Use of conductive surfaces and electrical grounding will allow static charge to dissipate. The continuity of electrical grounds should be verified according to the hyperbaric chamber manufacturing specifications or hospital requirements. .
- If it produces static, can the dressing, product or device be grounded?
- If it produces static, has the continuity of the chamber and electric grounds been verified?
|
Does it have a low flash point? | - If the Safety Data Sheet (SDS) of the item is not available, search for the SDS of the main component(s) of the item being evaluated (e.g., there is no flash point data in the SDS for Xeroform, but there is a flash point in the SDS for petroleum jelly)
- In all hyperbaric environments, the partial pressure of oxygen is higher than at normal atmospheric conditions. Increasing the partial pressure of oxygen can change the classification of a material from non flammable to flammable. Some materials burn more readily in a pressurized, 100% oxygen environment.
- Any material used in a hyperbaric chamber should have an ignition temperature higher than it can be exposed to. Paragraph 14.2.9.3.11 limits electrical equipment inside a Class A (multiplace) chamber to a maximum operating surface temperature of 85°C (185°F). Paragraph 14.2.9.6.3 limits electrical circuits inside a Class B (monoplace) chamber to a maximum operating temperature of 50°C (122°F). As the oxygen percentage increases, it takes less energy to ignite materials. This leads to more conservative decisions in a 100 percent oxygen environment. A greater margin of safety is achieved when there is a greater difference between the temperature limit of the equipment inside a Class A and B chamber and the ignition temperature of material in question.[1]
- A material will release vapor into the chamber environment as it approaches its flash point temperature. Once a sufficient quantity of vapor is present in the chamber (LEL), it takes very little energy for ignition to occur. Paragraph 14.3.1.6.2.2 sets limits on flammable agents inside Class A (multi-place) chambers. Paragraph 14.3.1.6.2.3 specifically prohibits flammable liquids, gases, and vapors inside Class B (monoplace) chambers. Information on ignition temperature and flash point in air can be found in a product SDS.[1]:
|
Is there too much fuel? | - Is the total fuel load too high? If a fire does occur, the energy produced is a function of the partial pressure of oxygen and the total fuel load. In a hyperbaric environment, the partial pressure of oxygen is higher and contributes to greater energy production. Any dressing product placed inside of a hyperbaric chamber is a combustible material and, therefore, adds to the fuel load. Therefore, total fuel load inside the chamber should be minimized to only what is necessary.
- If too much fuel, have you limited the quantity of fuel load (e.g, dressings, sheets, blankets, pillows, etc.)?
|
Are there any adverse effects? | - There can be other drug interactions with hyperbaric oxygen that are undesirable. For instance, it has been reported that the antibacterial agent mafenide acetate (Sulfamylon®), in combination with hyperbaric oxygen, has a poorer clinical result than either one by itself. The mechanical effects of pressure change can cause a dressing material to rupture.
|
Mechanical risk? | - Mechanical hazards include anything that leads to:
- Undesired release of compressed gas from the chamber: even small volumes of compressed gas represent a large amount of potential energy. Should this energy be released suddenly, the effects on adjacent structures and personnel can be devastating. The release could be a result of failure of the vessel or the associated piping, or if the chamber is modified in a manner contrary to the original code or standard of design and construction.
- Impaired access: any restriction on escape or impedance to rescue and firefighting efforts posed by the chamber create a hazard in case of an emergency.
- Reduced visibility through the chamber: reduction or restriction of vision of chamber operators reduces their effectiveness as safety monitors (e.g. an external fixator that scratches the chamber acrylic window)
- Collapse or rupture during changes in pressures: for instance, sealed or semi-sealed containers that are not adequately vented left inside the chamber will either collapse under pressure (possibly resulting in adiabatic heating of the contents and thus imposing a fire or explosion risk); or explode on resurfacing if the gas trapped within the container cannot escape during the ascent
- Malfunction, disruption or inoperativeness of many standard items when placed in service under hyperbaric conditions: includes the implosion of lamps and vacuum tubes (e.g., cathode ray tubes in medical monitors), overloading of fans due to a higher gas density, inaccurate operation of flow meters, pressure gauges and regulators.
|